High-Quality Activated Alumina for Catalyst Carrier Now Available at CHEMXIN-en.com
By:Admin
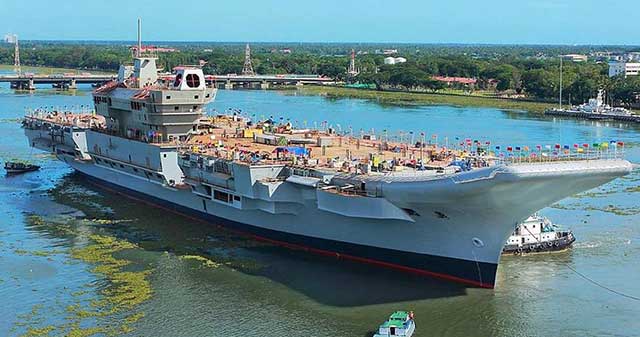
Activated alumina is a porous material with a high surface area, which makes it an ideal support material for catalysts. The material has excellent thermal stability, chemical inertness, and mechanical strength, making it highly resistant to temperature changes, chemical corrosion, and wear and tear. Activated alumina's unique properties make it an ideal choice for catalyst applications across a wide range of industries, including petrochemicals, pharmaceuticals, fine chemicals, and others.
CHEMXIN is a renowned manufacturer and supplier of activated alumina products, including activated alumina for catalyst carriers, molecular sieve, activated carbon, and other adsorbents and desiccants. The company has been providing high-quality products to the industry for over a decade, and its expertise in the field has earned it a reputation as a reliable and trusted supplier.
The company has a wide range of activated alumina products in stock, including different grades and sizes to cater to varying customer needs. The activated alumina for catalyst carriers is available in bead and sphere forms, with a typical surface area of 300-400 m²/g, pore volume of around 0.45-0.50 mL/g, and a bulk density of 0.70-0.75 g/cm³. CHEMXIN's activated alumina for catalyst carriers is made from high-purity aluminum oxide using a unique activation process that increases surface area, pore volume, and adsorption capacity.
The company's activated alumina products have been extensively tested and meet international quality standards, including ISO 9001:2015, RoHS, REACH, and other certifications. The products undergo strict quality control measures, including in-house testing and third-party testing, to ensure consistent and reliable quality.
CHEMXIN's activated alumina for catalyst carriers is competitively priced, which makes it an economical choice for users. The company's commitment to quality and customer satisfaction has helped it build long-term partnerships with customers across the globe. The company has a dedicated team of technicians and engineers who provide technical support and assistance to customers, helping them choose the right product for their specific application requirements.
In conclusion, CHEMXIN is a reputable and leading manufacturer and supplier of activated alumina for catalyst carriers. The company offers a wide range of high-quality products in different grades and sizes to meet varying customer needs. The products are competitively priced, made from high-purity materials, and meet international quality standards. With a commitment to quality and customer satisfaction, CHEMXIN is a trusted supplier to the industry, helping businesses enhance their catalytic processes and achieve greater efficiency.
Company News & Blog
The Impact of Catalyst on Tail Gas during Vanadium-Titanium Magnetite Carbon-Containing Pellet Reduction | E3S Web of Conferences
Vanadium-titanium magnetite, a kind of iron ore, is widely used in the production of steel due to its high iron content and strong magnetism. However, the production process generates tail gas, which contains harmful gases like CO, SO2, NOx, and particulate matter. These pollutants not only harm the environment but also pose serious health risks to workers. Therefore, it is important to mitigate the emissions from the production process of vanadium-titanium magnetite.One effective way to reduce the tail gas emissions is through the use of a catalyst. A catalyst is a substance that speeds up a chemical reaction without being consumed in the process. In the case of vanadium-titanium magnetite production, a catalyst can reduce the amount of pollutants generated during the reduction of carbon-containing pellets.Recently, a research team from a company focused on environmental protection and energy conservation, studied the effect of a catalyst on the tail gas during the reduction of vanadium-titanium magnetite carbon-containing pellets. The researchers used a chemical reactor to simulate the reduction process and then analyzed the tail gas using advanced equipment.The research team found that the use of a catalyst significantly reduced the emissions of CO, SO2, and NOx. The reduction rates of these pollutants were 64.3%, 75.4%, and 31.2%, respectively, compared to the process without a catalyst. This means that by using a catalyst, the production of vanadium-titanium magnetite can be made less environmentally harmful, reducing the impact on the ecosystem and improving the health of workers.Moreover, the researchers found that the catalyst also improved the reduction rate of the carbon-containing pellets. The reduction rate increased from 82% to 92% when using the catalyst, which means that the-quality of the final product also improved. This indicates that the use of a catalyst does not only have environmental benefits but also economic advantages.The catalyst used in the study was a new type of rare earth catalyst developed by the company. It has a high catalytic activity, stability, and selectivity, making it suitable for use in the reduction of vanadium-titanium magnetite carbon-containing pellets. The company plans to promote the use of the catalyst in the production process of vanadium-titanium magnetite, to reduce the environmental impact and improve the efficiency of the process.Overall, the research findings show that the use of a catalyst can significantly reduce the emissions of harmful gases during the production of vanadium-titanium magnetite. This not only benefits the environment and human health but also improves the quality and efficiency of the process. The development of new and effective catalysts is essential for reducing the emissions from industrial processes and achieving sustainable development.
Get Quality Activated Alumina for Catalyst Carriers at Low Prices from Professional Manufacturers
Low-Priced Activated Alumina for Catalyst Carrier Manufacturers - Stocked Activated Alumina for Catalyst Carrier - Wholesale Quality Products from Professional Manufacturers at CHEMXIN
As the global demand for sustainable and environmentally responsible industrial processes grows, the manufacture of high-quality catalyst carriers becomes increasingly important. Catalyst carriers are essential to the functioning of catalytic processes, which are used in various industries, including chemical, petroleum, and pharmaceuticals. The use of activated alumina as a catalyst carrier is a widely accepted practice throughout the industry due to its high surface area, pore volume, and surface hydroxyl groups. At CHEMXIN, we are proud to stock a wide range of quality activated alumina for catalyst carriers from leading manufacturers, providing our clients with reliable and cost-effective solutions.CHEMXIN is a respected supplier of activated alumina powder and ceramic balls, molecular sieves, and various adsorbents and catalyst carriers. With over 15 years of experience in the industry, we have built an extensive network of supply chains and adopted state-of-the-art manufacturing techniques to deliver high-quality products to our clients worldwide. Our activated alumina products are manufactured using high-grade raw materials and subjected to stringent quality control procedures to ensure they meet the highest industry standards.We recognize that our clients' requirements vary depending on the nature of their operations and production capacity. That's why we offer a wide range of activated alumina products that cater to different applications, including catalyst carriers, gas drying, water purification, and more. Our activated alumina powder is available in various sizes and shapes, making it easy for our clients to select the optimal particle size for their specific needs. We also offer customized solutions for clients who require specific sizes or shapes for their applications.Our activated alumina for catalyst carrier products has been tested and proven to offer superior performance and durability compared to other alternative options. The activated alumina's high pore volume and surface area provide a high capacity for adsorption, making it an effective carrier for catalysts. The activated alumina also has a high crushing strength, which enables it to withstand the rigors of industrial processes, ensuring long service life.One of the advantages of sourcing activated alumina for catalyst carrier products from CHEMXIN is the cost-effectiveness of our offerings compared to other suppliers. We work closely with our manufacturers to streamline the production processes and minimize overhead costs, allowing us to offer our clients competitive prices without compromising the quality of our products. Our clients can order activated alumina for catalyst carrier products in large volumes and enjoy discounts, further reducing their operational costs.At CHEMXIN, we understand the importance of timely and reliable delivery of goods to our clients. We have implemented a comprehensive logistics system that ensures our clients receive their orders on time and in excellent condition. Our products are packed in tamper-evident bags or drummed to prevent contamination during transportation, providing peace of mind to our clients.In conclusion, CHEMXIN is a trusted supplier of activated alumina for catalyst carrier products, offering a comprehensive range of quality products. Our commitment to excellence is demonstrated through our adherence to strict quality control procedures, competitive pricing, and reliable delivery of goods. We invite potential clients to visit our website and browse our catalog to find the activated alumina for catalyst carrier products that suit their specific needs.
Mechanistic Insights into DME Conversion over ZSM-5 Catalysts
and Dimethyl Ether (DME)ZSM-5 catalysts play a significant role in the conversion of dimethyl ether (DME) to olefins. This reaction is an important step in the production of valuable chemical compounds. However, the mechanism of this transformation has been elusive due to the complex nature of the reaction. In a recent study, researchers used temperature-programmed surface reaction experiments and microkinetic modelling to decouple the rates of adsorption, desorption, and surface reaction of DME over fresh and working ZSM-5 catalysts with different Si/Al ratios.The study yielded important insights into the reaction mechanism. The researchers discovered that propylene is the major olefin formed during the transformation of DME. They also observed site-specific scaling relations between the activation energies of DME desorption and barriers to the formation of methoxymethyl and methyl propenyl ether. Six ensembles of sites were observed, with a maximum of three adsorption/desorption sites and three adsorption/desorption/reaction sites.Interestingly, the researchers found that barriers were generally higher for working catalysts than fresh catalysts. This could have implications for industrial processes that use ZSM-5 catalysts.The study’s results were obtained by simulating transient reactor performance through the solving of coupled 1D nonlinear partial differential equations. This accounted for elementary steps during the induction period, based on the methoxymethyl mechanism on the zeolite catalyst, and axial dispersion and convection in the reactor. The activation energies of propylene formation were found to be approximately 200 kJ mol1, which corroborated direct mechanistic proposals.Overall, this study provides valuable mechanistic insights into the conversion of DME over ZSM-5 catalysts. The researchers’ use of temperature-programmed surface reaction experiments and microkinetic modelling allowed for decoupling the complex rates of the reaction, providing important information about site-specific mechanisms. This information may prove useful for developing more efficient and effective industrial processes that utilize ZSM-5 catalysts.In conclusion, the study underscores the importance of understanding the mechanistic details of catalytic reactions. By using advanced experimental and modelling techniques, we can gain insights that will allow for the development of more efficient and sustainable industrial processes.
Understanding Alumina: Properties and Uses
Alumina, a chemical compound with the molecular formula Al2O3, is a major industrial ceramic material used in the manufacturing of refractories, abrasives, and electronic components. It is a white or greyish-white powder that is derived from bauxite ore and is known for its high melting point, superior electrical insulation, and excellent mechanical strength.The alumina market is highly competitive with players like Alcoa, Rio Tinto, BHP Billiton, and Norsk Hydro dominating the industry. One of the leading producers of alumina is () - a global leader in the production of industrial minerals.The company has a diverse product portfolio that includes high-quality alumina products used in various industries such as ceramics, refractories, and electronics. Their alumina products are known for their exceptional chemical and mechanical properties, which makes them ideal for a wide range of applications.The alumina products offered by () are manufactured using advanced processes that ensure consistent quality and purity. Their range of alumina products includes Tabular Alumina, Calcined Alumina, Reactive Alumina, and Alumina Hydrates.Tabular Alumina is a high-purity form of alumina that is produced by sintering specially selected raw materials at high temperatures. It has excellent dimensional stability, mechanical strength, and thermal shock resistance, making it perfect for use in refractory applications.Calcined Alumina, on the other hand, is produced by calcining alumina hydroxide at high temperatures. It is used in ceramics, abrasives, and polishing applications due to its high hardness, chemical resistance, and excellent thermal conductivity.Reactive Alumina is a high-purity form of alumina that is used in the manufacturing of advanced ceramic products. This type of alumina is produced by a unique process that ensures the formation of small, uniform particles with superior chemical and mechanical properties.Alumina Hydrates are used as a flame retardant in the manufacturing of plastics, rubber, and textiles. () produces a range of Alumina Hydrates with varying particle sizes and degrees of hydration.The company has dedicated research and development facilities that focus on the development of new and advanced alumina products. Their R&D team works closely with customers to understand their specific requirements and develop tailored solutions that meet their needs.In addition to their extensive product portfolio, () is committed to sustainable practices and responsible mining. They have implemented environmental management systems that ensure the protection of the environment and the conservation of natural resources.The alumina market is expected to grow in the coming years due to the increasing demand for high-performance ceramics and electronic components. () is well-positioned to capitalize on this growth with its advanced product portfolio and commitment to sustainability.In conclusion, () is a leading producer of high-quality alumina products that are used in various industries. Their advanced manufacturing processes, commitment to sustainability, and dedicated R&D facilities make them a preferred partner for customers looking for tailored solutions to meet their specific needs.
Versatile Applications of Microspheres in Cementitious Systems, Composites and Polymer Materials
What Are Alumina Microspheres and Their Importance in Various Industries?Alumina Microspheres, also known as Cenospheres, are lightweight, thin-walled, hollow ceramic spheres composed mainly of alumina and silica, and are typically below 300 microns in size. These unique characteristics make them highly effective in a range of industrial applications across multiple industries.The low bulk density and high strength of alumina microspheres are crucial to their success in the manufacturing industry. They are an essential component of cementitious systems, putties, and sealants. In these products, they modify rheology, reduce weight and shrinkage, and improve thermal insulation properties. Because of these benefits, they are also used in composites and other polymer applications, where they reduce resin demand and improve impact resistance and strength.Specialized alumina microsphere grades are used in industries that require rigorous application conditions. For example, refractories and surface coatings utilize industrial-grade microspheres for coating applications. These coatings provide superior heat resistance, making them ideal for use in high-temperature conditions.Several end-user industries use Alumina Microspheres due to their unique properties. The plastics and gel-coats industry uses these microspheres in polyurethane, latex emulsions, PVC, and Epoxy resins. They are also frequently used in oil-well cements, dry-mix adhesives, and mortars.One major advantage of Alumina Microspheres is their ability to reduce weight and shrinkage in cementitious products. This crucial factor allows manufacturers to create lighter, stronger, and more durable products while saving on production costs.In composites, the incorporation of Alumina Microspheres improves the mechanical performance of the final product, and reduces weight and cost. Additionally, they can be used in high-temperature applications because of their superior resistance to heat.In surface coatings, Alumina Microspheres help improve the wear and tear resistance of the final product. Additionally, thermal insulation properties of the coating prevent heat loss from the surface.In summary, Alumina Microspheres offer several unique advantages to manufacturers across numerous industries. Their low bulk density and high strength make them ideal for enhancing the performance of cementitious, composite, and coating products. Their versatility and applicability in various industries make them a valuable resource for manufacturers and end-users alike.
Catalysts for Methanation: Converting Carbon Oxides and Hydrogen to Methane and Water
s and Nickel CatalystsMethanation Catalysts and Nickel Catalysts - A Complete GuideMethanation is a chemical process that is widely used in industrial applications, especially in the production of methane gas and purification of synthesis gas. The process is catalyzed by methanation catalysts, with nickel catalysts being the most commonly used in the industry. In this blog, we will dive deeper into methanation catalysts and nickel catalysts, their properties, and their applications.What are Methanation Catalysts?Methanation catalysts are substances that facilitate the conversion of carbon oxides and hydrogen into methane and water. The process occurs through a series of steps, including the adsorption of carbon oxides and hydrogen on the catalyst surface, the formation of intermediate compounds, and the final conversion to methane. Methanation catalysts are used in several industrial applications, including:1. Manufacturing of MethaneMethanation catalysts are commonly used in the production of methane from a carbon dioxide and hydrogen mixture. The process involves passing the mixture over a nickel methanation catalyst at high temperatures and pressures, resulting in the production of methane and water.2. Purification of Synthesis GasSynthesis gas is a mixture of carbon monoxide, carbon dioxide, and hydrogen, which is used as a feedstock in several chemical processes. However, synthesis gas must be purified before use, as it contains traces of carbon oxides that can damage downstream equipment. Methanation catalysts are used to remove carbon oxides from synthesis gas, converting them to methane and water.Properties of Methanation CatalystsThe properties of methanation catalysts vary depending on their composition, preparation method, and application. Generally, methanation catalysts should possess the following properties:1. High ActivityMethanation catalysts should have high activity in converting carbon oxides and hydrogen to methane, to increase the rate of reaction and reduce the contact time.2. SelectivityMethanation catalysts should be selective, converting carbon oxides to methane while minimizing undesirable side reactions.3. StabilityMethanation catalysts should be thermally stable and resistant to deactivation by poisons, such as sulfur and carbon.4. Low CostMethanation catalysts should be affordable and readily available, to reduce the cost of production.Nickel CatalystsNickel catalysts are the most commonly used methanation catalysts, due to their high activity and selectivity. Nickel catalysts can be prepared through several methods, including impregnation, precipitation, and co-precipitation. The choice of preparation method depends on the desired properties of the catalyst.Nickel catalysts have several advantages, including:1. High ActivityNickel catalysts are highly active in converting carbon oxides and hydrogen to methane, due to their unique structure and electronic properties.2. SelectivityNickel catalysts are selective, converting carbon oxides to methane while minimizing undesirable side reactions.3. Thermal StabilityNickel catalysts are thermally stable and resistant to deactivation by poisons, such as sulfur and carbon.4. AffordableNickel catalysts are affordable and readily available, making them an attractive choice for industrial applications.ConclusionMethanation catalysts and nickel catalysts are essential components in the production of methane and purification of synthesis gas. Methanation catalysts facilitate the conversion of carbon oxides and hydrogen to methane and water, while nickel catalysts are the most commonly used methanation catalysts due to their high activity and selectivity. The choice of catalyst depends on the desired properties and application of the catalyst. However, both methanation catalysts and nickel catalysts are essential in the chemical industry, contributing to the production of numerous chemical compounds.
Applications and Benefits of Microspheres in Various Industries
Applications of Alumina MicrospheresAlumina microspheres, also known as ceramic microspheres, are thin-walled hollow spheres made of alumina. With particle sizes ranging from 1 to 200 microns, these microspheres possess low bulk density, high compressive strength, and excellent thermal stability. Owing to their unique properties, alumina microspheres have become increasingly popular in various applications. In this blog post, we shall discuss some of the most significant applications of alumina microspheres.1. Refractory MaterialsAlumina microspheres are widely used in the manufacture of refractory materials. These microspheres act as filler materials in the production of refractory bricks, castables, and cements. They help to improve the mechanical strength, abrasion resistance, and thermal shock resistance of refractory products. Moreover, the use of alumina microspheres in refractory materials also helps to reduce the overall density of the product.2. Thermal Insulation MaterialsAnother key application of alumina microspheres is in the production of thermal insulation materials. Alumina microspheres possess excellent thermal insulation properties, which make them ideal for use in the production of thermal insulation coatings, foams, and composites. These coatings and composites are used in a range of industrial applications, such as aerospace, automotive, and construction.3. Polymer CompositesAlumina microspheres are also used as fillers in polymer composites. The addition of alumina microspheres to polymer matrices enhances the mechanical and thermal properties of the resulting composite. The microspheres help to improve the tensile and flexural strength, impact resistance, and thermal conductivity of the polymer composite.4. CeramicsAlumina microspheres are used in the production of ceramic materials, such as tiles, sanitary ware, and insulators. The microspheres are added to ceramic formulations to improve the mechanical properties and reduce the overall density of the product. Additionally, alumina microspheres can be used as sintering aids, helping to promote densification during the firing process.5. Environmental RemediationAlumina microspheres are also used in environmental remediation applications, such as groundwater remediation, heavy metal removal, and oil spill cleanup. The microspheres can be coated with chemicals or functional groups that help to selectively adsorb contaminants from the environment. The hollow structure of the microspheres also allows for the encapsulation of contaminants, making them easier to remove and dispose of.ConclusionAlumina microspheres are versatile materials with numerous applications across various industries. Whether it is in the manufacture of refractories, thermal insulation materials, polymer composites, ceramics, or environmental remediation, alumina microspheres have proven to be valuable additives. As research continues, it is likely that new applications for these microspheres will emerge, making them even more useful in various fields.
Catalyst's Impact on Tail Gas in Vanadium-Titanium Magnetite Carbon-Containing Pellet Reduction | Proceedings in Environmental, Energy, and Earth Sciences
Vanadium-titanium magnetite (VTM) carbon-containing pellets are widely used in iron and steel production. However, the production process generates tail gas containing high levels of pollutants such as carbon monoxide (CO) and sulfur dioxide (SO2). These pollutants not only harm the environment but also impact the quality of the final product. To address this problem, researchers have studied the effect of a hydrogenation catalyst on tail gas during the reduction of VTM carbon-containing pellets.The hydrogenation catalyst is a substance that promotes the hydrogenation reaction, i.e., the addition of hydrogen to a substance. In this case, the catalyst promotes the reduction of CO and SO2 in the tail gas to harmless substances like carbon dioxide (CO2) and sulfuric acid (H2SO4). The researchers used a fixed-bed reactor to measure the effect of the catalyst on tail gas.The results showed that the addition of the hydrogenation catalyst significantly reduced the levels of CO and SO2 in the tail gas. The catalyst also increased the yield of H2SO4 from SO2. The researchers found that the optimal conditions for hydrogenation catalyst were a temperature of 200 °C, a hydrogen flow rate of 240 mL/min, and a catalyst bed height of 5 cm. Under these conditions, the reduction rates of CO and SO2 were 95.5% and 92.6%, respectively.The researchers also studied the mechanism by which the hydrogenation catalyst reduces CO and SO2. They found that the catalyst first adsorbed the CO and SO2 molecules on its surface. Then, the hydrogen molecules dissociated on the catalyst surface and reacted with the adsorbed CO and SO2 molecules to form CO2 and H2SO4, respectively. The adsorbed CO and SO2 molecules were completely consumed in the reaction.The results of this study have important implications for the iron and steel industry. The use of a hydrogenation catalyst can effectively reduce the amount of pollutants in tail gas and improve the quality of the final product. The researchers suggest that future studies should focus on the development of more efficient and economical hydrogenation catalysts.In conclusion, the effect of a hydrogenation catalyst on tail gas during the reduction of VTM carbon-containing pellets has been studied, and significant reductions in the levels of CO and SO2 have been observed. The researchers suggest that the use of hydrogenation catalysts can be an effective means of reducing pollutants in tail gas, which has important implications for the iron and steel industry. The keywords "Tail Gas Hydrogenation Catalyst" may help promote this research and enhance its academic influence.