Pentasil Zeolite: Properties, Uses, and Applications
By:Admin
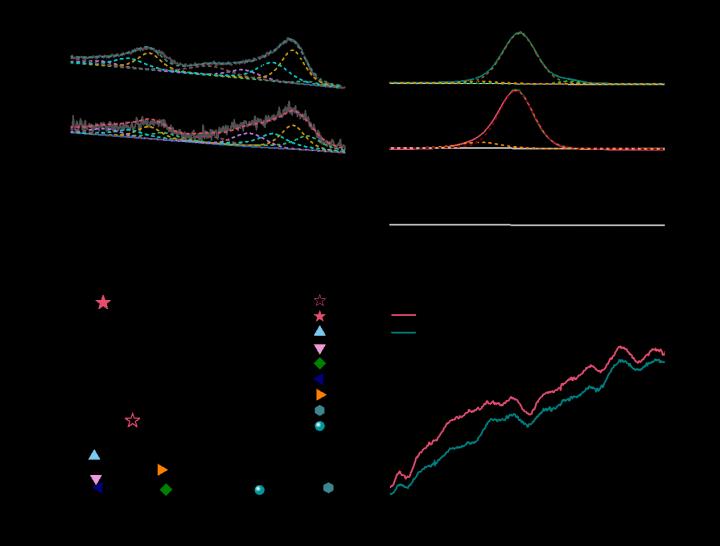
The chemical formula for ZSM-5 is NaAlSiO16HO (0
Patented by Mobil Oil Company in 1975, ZSM-5 has since been widely used as a heterogeneous catalyst in the petroleum industry. It is well-known for its ability to selectively produce gasoline-range molecules from larger alkanes and olefins.
One of the unique features of ZSM-5 is its high acidity, which is due to the presence of aluminum within its crystal structure. This acidity gives ZSM-5 its catalytic properties and plays a critical role in its ability to isomerize hydrocarbons.
ZSM-5 also has the ability to shape-selectively catalyze reactions due to its unique pore structure. This means that certain molecules can selectively enter the pores of ZSM-5, allowing for the catalysis of specific reactions.
Due to its catalytic properties, ZSM-5 has been used in a variety of applications beyond the petroleum industry. It has been used in the production of fine chemicals, such as flavors and fragrances, as well as in the production of biofuels.
In conclusion, ZSM-5 is an important zeolite used in the catalysis of hydrocarbon isomerization reactions. Its unique pore structure and high acidity make it useful in a variety of applications beyond the petroleum industry, including the production of fine chemicals and biofuels. With continued research and development, ZSM-5 has the potential to play an even larger role in the future of catalysis.
Company News & Blog
Study Shows ZSM-5 Zeolite's Potential Benefits
Introducing a Breakthrough in Catalyst Technology: ZSM-5Catalysts play a critical role in a wide range of chemical processes, including the production of fuels, chemicals, and environmental cleanup. These materials help to speed up the rate of chemical reactions and improve the efficiency of these processes. With the importance of catalysts in mind, [Company Name] has been dedicated to the research and development of innovative catalyst technologies for over a decade. The latest breakthrough from [Company Name] comes in the form of a new generation of catalysts based on the zeolite ZSM-5.ZSM-5 is a type of zeolite, a crystalline material with a unique porous structure that makes it an ideal candidate for catalytic applications. The use of ZSM-5 as a catalyst has long been recognized for its potential to improve the selectivity and activity of various chemical reactions. However, [Company Name] has taken this a step further by developing a proprietary method for synthesizing ZSM-5 with enhanced properties, making it an even more effective catalyst for a range of industrial processes.The unique properties of the new ZSM-5 catalyst developed by [Company Name] have been demonstrated in several key applications. For example, in the field of petroleum refining, the new catalyst has shown exceptional performance in converting bulky hydrocarbons into more valuable products such as gasoline and diesel fuel. This has the potential to significantly improve the efficiency and economics of refinery operations, providing a competitive advantage for companies in the petroleum industry.In addition to petroleum refining, the new ZSM-5 catalyst has also shown promise in the production of chemicals and petrochemicals. For example, it has demonstrated high activity and selectivity in the conversion of methanol to olefins, a key reaction for the production of plastics and other materials. By improving the efficiency of this process, the new catalyst has the potential to reduce production costs and increase the sustainability of chemical manufacturing.Furthermore, the unique structure of the new ZSM-5 catalyst has also shown potential in environmental applications. For example, it has been demonstrated to be highly effective in the catalytic conversion of harmful pollutants such as nitrogen oxides and volatile organic compounds into more benign substances. This makes it a promising candidate for use in exhaust treatment systems for vehicles and industrial facilities, helping to reduce air pollution and improve air quality.In summary, the new generation of ZSM-5 catalyst developed by [Company Name] represents a significant advancement in catalyst technology. Its improved performance and versatility make it a valuable tool for a wide range of industrial processes, from petroleum refining to chemical production and environmental remediation. With this breakthrough, [Company Name] is poised to make a meaningful impact on the global chemical industry and contribute to a more sustainable and efficient future.For more information about [Company Name] and its innovative catalyst technologies, please visit www.companywebsite.com.Contact:[Company Name]Phone: XXX-XXX-XXXXEmail: [email protected]
New Methanation Catalyst Could Revolutionize Renewable Energy Production
Methanation Catalyst, a revolutionary new product in the field of chemical production, has been introduced by a leading chemical company. This innovative solution is designed to help industries address the challenges of producing clean energy by utilizing carbon dioxide and renewable hydrogen to produce methane. The new catalyst is a game-changer for industries looking for sustainable ways to produce clean fuels, and it is set to transform the way we produce energy.The Methanation Catalyst is a high-performance catalyst that significantly improves the efficiency of the methanation process, where carbon dioxide and renewable hydrogen are chemically transformed into methane. The catalyst is formulated to have a high activation energy, which enables it to speed up the methanation reaction significantly. This breakthrough product has already been integrated into several industrial processes, such as ammonia production and gas-to-liquid processes.The Methanation Catalyst is composed of several key ingredients that enable it to perform efficiently. These ingredients include a unique support structure that helps to facilitate the carbon dioxide reduction reaction. The catalyst also contains active metal sites that promote the hydrogenation of carbon dioxide, which is critical to the methanation process.According to leading industry experts, the Methanation Catalyst is an important solution to the challenges that industries face with conventional methanation processes. This new catalyst provides industries with a sustainable method of producing clean energy by harnessing renewable hydrogen and carbon dioxide. The catalyst is also cost-effective, which is a significant advantage for companies operating in competitive markets.The Methanation Catalyst has already been tested in several industrial processes and has demonstrated exceptional results. In large-scale ammonia production, the catalyst increased the conversion rate of carbon dioxide to methane while reducing the energy required for the methanation process. The performance of the catalyst in these tests has demonstrated that Methanation Catalyst is a reliable and efficient solution for industries.Methanation Catalyst is also playing an important role in the transition to green energy. The demand for cleaner energy sources continues to increase globally, and this product provides a solution. The catalyst allows industries to produce a clean, renewable, and sustainable source of energy, ultimately contributing to the goal of creating a more sustainable future.The supply of hydrogen is critical for the methanation process, and industries require a reliable and sustainable source of hydrogen to produce high-quality methane. The Methanation Catalyst enables industries to utilize renewable hydrogen produced from various sources such as solar and wind power. This is an important step towards achieving net-zero carbon emissions, and the Methanation Catalyst is a crucial technology that will support this transition.The Methanation Catalyst is just one of the many innovative solutions developed by leading chemical companies to help reduce carbon emissions and support the transition to clean energy. The company that has introduced Methanation Catalyst is a world-renowned leader in the development and production of high-quality catalysts and has a long-standing track record of delivering excellent products and services to the chemical industry.The introduction of Methanation Catalyst is a significant milestone for the industry, and it is poised to transform the way we produce energy. The product represents a new era in sustainable energy production, and it is one of the innovative solutions that industries can utilize to reduce their carbon footprint. The Methanation Catalyst is not only a solution for energy production; it is also an example of how innovative technology can be utilized to create a more sustainable and cleaner future for everyone.In conclusion, the introduction of Methanation Catalyst is a significant achievement for the chemical industry, and it is set to revolutionize the way we produce energy. The product offers a sustainable and reliable solution to the challenges of methanation and provides a path towards a sustainable and carbon-neutral future. With Methanation Catalyst, industries have a tool to produce clean energy sustainably while addressing the challenges of climate change.
Highly Effective Catalyst for Chemical Reactions: ZSM-5 Catalyst Explained
ZSM-5 Catalyst Shows Promising Results in Petrochemical IndustryThe petrochemical industry is constantly seeking innovative technologies to improve the efficiency and sustainability of their processes. One such advancement that has been making waves in the industry is the ZSM-5 catalyst, which has shown promising results in various applications within the petrochemical sector. This catalyst, developed by a leading company in the field of catalysis and process technology, has garnered significant attention for its potential to revolutionize the production of chemicals and fuels.The ZSM-5 catalyst, a member of the zeolite family, has unique properties that make it a highly effective and versatile component in petrochemical processes. Its high surface area, acidity, and shape-selective properties make it particularly well-suited for catalyzing a wide range of reactions, including hydrocracking, isomerization, and aromatization. These capabilities have led to its widespread use in the production of gasoline, petrochemical intermediates, and other valuable products.One of the key advantages of the ZSM-5 catalyst is its ability to facilitate the conversion of low-value feedstocks into high-demand products. This not only helps petrochemical companies to maximize their yields and profits but also contributes to the sustainable utilization of resources. In addition, the catalyst’s performance stability and resistance to deactivation make it a reliable and cost-effective solution for industrial-scale operations.Furthermore, the ZSM-5 catalyst has shown great potential in the production of biofuels and renewable chemicals. Its ability to efficiently convert biomass-derived compounds into valuable products aligns with the industry’s increasing focus on sustainability and reducing its environmental footprint. By leveraging the unique properties of the ZSM-5 catalyst, petrochemical companies can diversify their feedstock options and contribute to the transition towards a more sustainable and circular economy.The company behind the development of the ZSM-5 catalyst has a strong track record in the field of catalysis and process technology. With decades of experience and a team of experts, the company has been at the forefront of developing innovative solutions for the petrochemical industry. Its commitment to research and development, coupled with state-of-the-art facilities and equipment, has enabled the company to deliver cutting-edge catalysts and process technologies that meet the evolving needs of its clients.Moreover, the company’s dedication to sustainability and responsible business practices is reflected in the design and production of its catalysts. By prioritizing energy efficiency, waste reduction, and environmental impact, the company ensures that its products contribute to a more sustainable and eco-friendly petrochemical industry. This commitment to sustainable innovation has cemented the company’s reputation as a trusted partner for petrochemical companies seeking to enhance their operations while minimizing their environmental footprint.As the petrochemical industry continues to evolve and adapt to changing market dynamics and environmental regulations, the demand for advanced catalysts such as the ZSM-5 catalyst is expected to grow. Its proven performance, versatility, and sustainability credentials make it a compelling choice for petrochemical companies looking to optimize their processes and stay ahead of the curve. With ongoing research and development efforts, the company behind the ZSM-5 catalyst is poised to further advance the capabilities of this groundbreaking technology and unlock new opportunities for the petrochemical industry.In conclusion, the ZSM-5 catalyst has emerged as a game-changer in the petrochemical industry, offering a potent combination of performance, versatility, and sustainability. As petrochemical companies continue to seek innovative solutions to improve their operations and reduce their environmental impact, the ZSM-5 catalyst stands out as a catalyst for change. With the support of the company behind its development, this catalyst is poised to play a pivotal role in shaping the future of the petrochemical industry.
Study Finds ZSM-5 Zeolite Catalyst Effective for Chemical Reactions
**Breakthrough in Chemical Engineering: Zsm-5 Catalyst Revolutionizes Petrochemical Industry**In a groundbreaking development in the world of chemical engineering, a new and highly efficient catalyst, Zsm-5, has been unveiled by a leading research company. This new catalyst has the potential to revolutionize the petrochemical industry, dramatically increasing the efficiency of various chemical processes and reducing environmental impact.Zsm-5 is a zeolite catalyst with a unique porous structure that allows for the selective adsorption and transformation of molecules. This innovative catalyst has already shown promising results in a wide range of applications, including the catalytic cracking of hydrocarbons, the conversion of methanol to hydrocarbons, and the production of various chemicals and fuels.The company behind this pioneering catalyst, has been at the forefront of chemical research and development for over two decades. With a team of highly skilled scientists and engineers, the company has dedicated itself to creating innovative solutions to address the pressing challenges facing the petrochemical industry.With a strong emphasis on sustainability and environmental stewardship, the company has made significant investments in research and development to create new catalysts and processes that can mitigate the environmental impact of the petrochemical industry.The introduction of Zsm-5 is a testament to the company's commitment to innovation and sustainability. This new catalyst has the potential to significantly reduce energy consumption and carbon emissions in various chemical processes, making a positive impact on the environment and the bottom line of companies in the industry.One of the most significant applications of Zsm-5 is in the catalytic cracking of hydrocarbons. This process is essential for the production of gasoline and other valuable fuels from crude oil. With the use of Zsm-5, this process can be made more efficient, leading to higher yields of valuable products and reduced energy consumption.Furthermore, Zsm-5 has shown great promise in the conversion of methanol to hydrocarbons, a process that is crucial for the production of chemicals and fuels from renewable sources. By using Zsm-5 as a catalyst, this conversion process can be made more efficient and cost-effective, paving the way for a more sustainable chemical industry.In addition to these applications, Zsm-5 also has the potential to revolutionize the production of various chemicals and fuels, offering a more sustainable and efficient alternative to traditional catalysts.The introduction of Zsm-5 has garnered significant attention from the petrochemical industry, with many companies expressing interest in adopting this innovative catalyst to improve their processes and reduce their environmental footprint.The impact of Zsm-5 is not limited to the petrochemical industry, as it has the potential to revolutionize other chemical processes and industries as well. With its unique properties and versatility, Zsm-5 could become a crucial catalyst in the transition towards a more sustainable and efficient chemical industry.As the company continues to advance its research and development efforts, the potential applications of Zsm-5 are expected to expand, opening up new possibilities for the petrochemical industry and beyond.In conclusion, the introduction of Zsm-5 represents a significant breakthrough in the world of chemical engineering. This innovative catalyst has the potential to revolutionize the petrochemical industry, offering more sustainable and efficient solutions to address the pressing challenges facing the industry. With its unique properties and versatility, Zsm-5 could play a crucial role in the transition towards a more sustainable and environmentally friendly chemical industry.
Sulfur Tolerant Shift Catalyst: An Innovative Solution for Emission Control
Sulfur Tolerant Shift Catalyst: Breaking New Ground in Environmental TechnologyThe global push for cleaner and more sustainable energy sources has led to significant advancements in technology aimed at reducing harmful emissions from industrial processes. One company at the forefront of this movement is {}, a leader in the development of innovative environmental solutions. One of their most recent breakthroughs is the development of a Sulfur Tolerant Shift Catalyst, which has the potential to revolutionize the way industries manage their emissions.{} has a long history of developing cutting-edge catalysts and technologies that address the environmental challenges facing the world today. With a team of dedicated researchers and a commitment to sustainability, the company has been able to consistently deliver innovative solutions that have a positive impact on the environment.The Sulfur Tolerant Shift Catalyst is the latest addition to their impressive portfolio of environmental technologies. This catalyst is specifically designed to address the issue of sulfur poisoning in shift reactors, which has been a major obstacle in the quest for more efficient and environmentally friendly industrial processes. By effectively mitigating the detrimental effects of sulfur, this catalyst has the potential to significantly improve the performance of shift reactors, leading to reduced emissions and a more sustainable operation.The innovative design of the Sulfur Tolerant Shift Catalyst leverages advanced materials and a sophisticated chemical composition to create a highly efficient and durable solution for sulfur poisoning. This breakthrough technology has been extensively tested and validated in real-world industrial settings, where it has demonstrated exceptional performance and reliability. The proven effectiveness of this catalyst has generated a great deal of interest and excitement within the industry, as it represents a major step forward in the quest for cleaner and more sustainable industrial processes.In addition to its impressive technical capabilities, the Sulfur Tolerant Shift Catalyst also offers practical benefits that make it an attractive solution for industries around the world. Its robust design and long operational life translate to lower maintenance costs and reduced downtime, while its superior performance results in higher process efficiency and lower emissions. These compelling advantages position this catalyst as a game-changing technology that has the potential to make a significant impact on the global environmental landscape.Furthermore, the development of the Sulfur Tolerant Shift Catalyst underscores {}'s ongoing commitment to advancing environmental sustainability through technological innovation. By focusing on the development of solutions that enable industries to operate in a more responsible and sustainable manner, the company is contributing to the global effort to reduce the environmental impact of industrial processes. This commitment is further evidenced by their comprehensive approach to developing and commercializing environmentally friendly technologies, encompassing rigorous testing, regulatory compliance, and ongoing support to ensure the successful implementation of their solutions.Looking ahead, the potential of the Sulfur Tolerant Shift Catalyst extends far beyond its immediate applications. As industries continue to seek more efficient and sustainable ways of operating, this breakthrough technology is poised to play a key role in shaping the future of industrial processes. By enabling a more effective management of emissions and fostering a more sustainable approach to production, this catalyst has the potential to drive positive change across a wide range of industries, ultimately contributing to a cleaner and healthier environment for future generations.In conclusion, the development of the Sulfur Tolerant Shift Catalyst represents a significant milestone in the quest for more sustainable industrial processes. With its exceptional performance, practical benefits, and long-term environmental impact, this catalyst has the potential to revolutionize the way industries manage their emissions and operate in a more responsible manner. As a leader in the development of innovative environmental technologies, {} continues to demonstrate its commitment to driving positive change and shaping a more sustainable future for the planet.
Effective Methanol Synthesis Catalyst: A Breakthrough in Chemical Engineering
Methanol Synthesis CatalystMethanol is a key building block in the chemical industry and is used in the production of a wide range of products, including plastics, adhesives, and fuels. One of the most crucial steps in the manufacture of methanol is the synthesis process, which requires a highly efficient catalyst to facilitate the reaction.Recently, a leading company in the field of catalyst development has made significant strides in the development of a novel methanol synthesis catalyst that promises to revolutionize the production of methanol. This innovative catalyst, referred to as Catalyst X, has been designed to offer exceptional activity and selectivity, enabling manufacturers to produce methanol with high efficiency and minimal waste.The company behind Catalyst X, {}, has been a pioneer in the development of catalysts for chemical processes for over 50 years. With a strong focus on research and development, the company has continually pushed the boundaries of catalyst technology to deliver solutions that address the evolving needs of the chemical industry.The development of Catalyst X is a testament to the company's commitment to innovation and its ability to leverage cutting-edge research and development capabilities to deliver game-changing solutions. By harnessing the power of advanced materials and engineering expertise, the company has succeeded in creating a catalyst that outperforms existing options in the market, offering unparalleled performance and reliability.What sets Catalyst X apart from traditional methanol synthesis catalysts is its unique formulation, which is tailored to promote the desired chemical reactions while minimizing unwanted by-products. This level of precision and control is critical in the production of methanol, as it directly influences the overall process efficiency and the quality of the end product.The superior performance of Catalyst X can be attributed to the meticulous design process that the company has employed. Through a combination of computational modeling, laboratory testing, and pilot-scale trials, the company's team of experts has fine-tuned the catalyst to deliver optimal results under a wide range of operating conditions.In addition to its exceptional performance, Catalyst X also offers enhanced durability, ensuring a longer operational lifespan and reduced maintenance requirements for methanol production facilities. This not only translates to cost savings for manufacturers but also contributes to a more sustainable and environmentally friendly production process.Furthermore, Catalyst X has been designed to be compatible with existing methanol synthesis technologies, allowing manufacturers to seamlessly integrate it into their current production processes without the need for extensive modifications. This ease of adoption makes Catalyst X an attractive option for companies looking to enhance the efficiency and competitiveness of their methanol production operations.Looking ahead, the company is poised to leverage its expertise in catalyst development to further advance the capabilities of Catalyst X and explore new applications in the field of chemical synthesis. With a strong emphasis on collaboration and co-innovation, the company remains committed to working closely with customers to address their specific challenges and develop tailored solutions that deliver tangible value.Overall, the development of Catalyst X marks a significant milestone in the evolution of methanol synthesis technology. With its unmatched performance, durability, and compatibility, Catalyst X is set to redefine the standards for methanol production and empower manufacturers to achieve new levels of efficiency and sustainability. As the company continues to drive innovation in catalyst development, the future looks bright for the chemical industry, with exciting possibilities on the horizon.
Innovative Catalyst Carrier Spheralite Technology: A Game-Changer in the Industry
Spheralite, a leading catalyst carrier provider, has announced the launch of their new and innovative product that is set to revolutionize the industry. The new catalyst carrier, which is yet to be named, is a game-changer in the world of catalytic technology. This breakthrough product is poised to transform the way catalysts are utilized in various industries, offering enhanced performance and efficiency.Spheralite, the company behind this groundbreaking development, has a long-standing reputation for producing high-quality catalyst carriers. With a wealth of experience and expertise in the field, Spheralite has consistently delivered innovative solutions that meet the evolving needs of their customers. The company's commitment to research and development has led to the creation of this new catalyst carrier, which promises to deliver unparalleled results.The new catalyst carrier boasts a range of impressive features that set it apart from traditional carriers. One of the key highlights of this product is its exceptional surface area, which allows for greater catalytic activity. This means that the catalyst can perform more efficiently, resulting in improved overall performance. Additionally, the new carrier offers excellent thermal stability, ensuring that it can withstand high temperatures without compromising its effectiveness.Furthermore, this innovative catalyst carrier has been designed to be highly versatile, making it suitable for a wide range of applications. Whether it's used in the petrochemical industry, environmental remediation, or chemical production, the new carrier is set to deliver exceptional results across the board. Its flexibility and adaptability make it an ideal choice for businesses looking to optimize their catalytic processes.In addition to its technical capabilities, the new catalyst carrier also offers environmental benefits. Spheralite has engineered the product to be more sustainable, with a focus on reducing energy consumption and minimizing environmental impact. This aligns with the company's commitment to sustainability and corporate social responsibility, as they strive to empower their customers to operate in a more eco-friendly manner.Spheralite has expressed their enthusiasm for the launch of this new catalyst carrier, emphasizing the hard work and dedication that has gone into its development. The company's spokesperson stated, "We are thrilled to introduce this game-changing product to the market. Our team has worked tirelessly to create a catalyst carrier that pushes the boundaries of what is possible in catalytic technology. We believe that this product will set a new standard for performance and efficiency, and we are excited to see the impact it will make across various industries."The launch of the new catalyst carrier represents a significant milestone for Spheralite, as they continue to solidify their position as a leader in the field of catalyst carriers. The company's ongoing commitment to innovation and excellence has positioned them as a trusted partner for businesses seeking cutting-edge solutions for their catalytic needs.As the new catalyst carrier prepares to make its debut in the market, industry professionals and businesses are eagerly anticipating its arrival. With its remarkable features and potential for widespread impact, it is expected to garner considerable interest and demand. Spheralite is gearing up to meet this demand and is ready to support their customers as they embrace this innovative technology.Overall, the introduction of the new catalyst carrier from Spheralite represents a significant step forward for the industry. With its advanced capabilities, versatility, and environmental benefits, this product is poised to elevate catalytic processes and drive efficiency across various sectors. As Spheralite prepares to unveil their latest innovation, the industry is abuzz with anticipation, eagerly awaiting the opportunity to experience the transformative power of this groundbreaking catalyst carrier.
Latest Innovation in Sulfur Recovery Catalyst Revealed
Claus Sulfur Recovery Catalyst is an essential component for sulfur recovery in various industries such as oil and gas, refining, and petrochemicals. This catalyst is designed to efficiently convert hydrogen sulfide (H2S) into elemental sulfur during the refining process, helping to reduce emissions and comply with environmental regulations.The Claus process, named after its inventor Carl Friedrich Claus, is the most commonly used method for sulfur recovery in the oil and gas industry. The process involves the thermal reduction of H2S to elemental sulfur using a series of catalytic converters, with the Claus Sulfur Recovery Catalyst playing a crucial role in this conversion.One company that has made significant strides in the development and production of high-quality Claus Sulfur Recovery Catalyst is {Company X}. With a focus on sustainability and innovation, {Company X} has emerged as a leader in the field of catalyst technologies for sulfur recovery. Their proprietary catalysts are designed to deliver superior performance, longevity, and cost-efficiency, making them the preferred choice for many refineries and petrochemical plants around the world.{Company X} is committed to providing innovative solutions that address the evolving needs of the industry while minimizing environmental impact. Their state-of-the-art research facilities and experienced team of scientists and engineers enable them to develop cutting-edge catalysts that optimize the sulfur recovery process and contribute to overall operational efficiency.In addition to their advanced catalyst technologies, {Company X} offers a comprehensive range of technical services to support their customers in maximizing the performance of their sulfur recovery units. From catalyst monitoring and optimization to troubleshooting and technical support, {Company X} is dedicated to ensuring that their customers achieve the highest level of sulfur recovery while adhering to stringent environmental standards.Furthermore, {Company X} is committed to sustainability and environmental responsibility. They continuously strive to develop catalysts and processes that minimize waste, reduce energy consumption, and lower emissions. By partnering with {Company X}, customers can align their sulfur recovery operations with the principles of sustainable development and make a positive impact on the environment.With a global presence and a strong network of distribution partners, {Company X} is well-positioned to cater to the diverse needs of the sulfur recovery market. Their commitment to excellence, reliability, and customer satisfaction has earned them a reputation as a trusted provider of sulfur recovery catalysts and technical solutions.In conclusion, Claus Sulfur Recovery Catalyst is an indispensable component for sulfur recovery in various industries, and {Company X} has established itself as a leading supplier of high-performance catalysts for this application. With a focus on innovation, sustainability, and customer support, {Company X} continues to drive advancements in sulfur recovery technologies, empowering their customers to achieve operational excellence while meeting their environmental objectives.
Highly Effective Gamma Alumina Catalyst for Industrial Applications
Gamma Alumina Catalysts: Revolutionizing the Oil and Gas IndustryIn the world of oil and gas production, efficiency and productivity are paramount. Companies are constantly searching for ways to streamline their processes and improve their bottom line. Enter Gamma Alumina Catalyst, a cutting-edge solution that is revolutionizing the industry.Gamma Alumina Catalyst, developed by a leading chemical company, is a high-performance catalyst that is specifically designed for use in oil and gas refining processes. The catalyst offers a wide range of benefits, including improved product yields, increased process efficiency, and reduced energy consumption. This innovative solution has quickly become a game-changer for companies looking to optimize their operations and stay ahead of the competition.The use of Gamma Alumina Catalyst has had a transformative impact on the industry, allowing companies to significantly enhance their production capabilities and achieve higher levels of output. By leveraging this advanced catalyst, companies are able to improve the quality of their products, reduce waste, and ultimately increase their profitability. This has made Gamma Alumina Catalyst a highly sought-after solution for companies in the oil and gas sector.One of the key advantages of Gamma Alumina Catalyst is its versatility. The catalyst is highly effective in a wide range of refining processes, including hydroprocessing, petrochemical manufacturing, and environmental protection. This flexibility has made it an invaluable tool for companies looking to improve their refining operations and address the unique challenges they face.Furthermore, the company behind Gamma Alumina Catalyst has a proven track record of delivering high-quality, innovative solutions to the oil and gas industry. With decades of experience and a commitment to excellence, the company has established itself as a trusted partner for companies looking to enhance their operations and achieve their business goals. This reputation for excellence has made Gamma Alumina Catalyst the catalyst of choice for some of the biggest players in the industry.In addition to its technical capabilities, the company places a strong emphasis on sustainability and environmental responsibility. The development of Gamma Alumina Catalyst reflects the company's commitment to creating solutions that not only improve efficiency and productivity but also minimize the environmental impact of oil and gas production. By using Gamma Alumina Catalyst, companies are able to reduce their carbon footprint and contribute to a more sustainable future for the industry.As the demand for Gamma Alumina Catalyst continues to grow, the company remains dedicated to pushing the boundaries of innovation and delivering new, advanced solutions to the market. With ongoing research and development efforts, the company is constantly working to improve the performance and capabilities of its catalyst, ensuring that it remains at the forefront of the industry.In conclusion, the introduction of Gamma Alumina Catalyst has had a profound impact on the oil and gas industry. By offering a versatile, high-performance solution for refining processes, the catalyst has enabled companies to enhance their productivity, improve their product quality, and achieve their business objectives. With a commitment to sustainability and a proven track record of excellence, the company behind Gamma Alumina Catalyst is poised to continue leading the way in delivering innovative solutions to the industry. As companies strive to optimize their operations and stay competitive in a rapidly evolving market, Gamma Alumina Catalyst stands out as a game-changing solution that is driving the industry forward.
Discover the Benefits of Using Alumina Catalyst for Your Catalyst Needs
Gamma Alumina Catalysts: A Game-Changer in Catalytic ProcessesCatalysis is an essential process in many industries such as petrochemical, environmental, and pharmaceutical. It involves the use of catalysts to accelerate chemical reactions, improve efficiency, and reduce energy consumption. One such catalyst that has been making waves in the industry is gamma alumina.Gamma alumina catalysts are a type of catalyst that is used in various catalytic processes. They are known for their high surface area, thermal stability, and excellent catalytic activity. These properties make gamma alumina catalysts an ideal choice for a wide range of applications.One company that has been at the forefront of developing and producing gamma alumina catalysts is {}. With over {} years of experience in the industry, they have established themselves as a reliable and innovative provider of catalyst solutions.The company's gamma alumina catalysts are widely used in the petrochemical industry for processes such as fluid catalytic cracking, hydrocracking, and reforming. Their catalysts have been proven to improve the yield and quality of products, reduce energy consumption, and enhance the overall efficiency of these processes.In addition to the petrochemical industry, {}'s gamma alumina catalysts are also used in environmental applications such as catalytic converters for automotive emissions control. These catalysts help to convert harmful pollutants such as carbon monoxide, nitrogen oxides, and hydrocarbons into less harmful substances, thereby reducing air pollution.Furthermore, {}'s gamma alumina catalysts are gaining traction in the pharmaceutical industry for the production of fine chemicals and pharmaceutical intermediates. The high surface area and catalytic activity of their catalysts make them well-suited for complex chemical transformations required in pharmaceutical manufacturing.{}'s commitment to research and development has enabled them to continuously improve their gamma alumina catalysts. They have invested in state-of-the-art facilities and a team of experienced scientists and engineers to develop innovative catalyst formulations and manufacturing processes.One of the key advantages of {}'s gamma alumina catalysts is their consistency and uniformity, which is crucial for achieving reliable and predictable results in catalytic processes. Their strict quality control measures ensure that each batch of catalyst meets the highest standards and performance requirements.Furthermore, {}'s technical support team works closely with customers to provide customized catalyst solutions tailored to their specific requirements. This collaborative approach has earned them a reputation for delivering value-added solutions and superior customer satisfaction.Looking ahead, {} is committed to addressing the ever-evolving needs of the industry by continuing to invest in research and development, expanding their product portfolio, and enhancing their manufacturing capabilities. They aim to further elevate the performance and versatility of gamma alumina catalysts to meet the growing demands of their customers.In conclusion, gamma alumina catalysts have become indispensable in catalytic processes across various industries, and {} has emerged as a leading provider of these catalysts. With a strong focus on innovation, quality, and customer satisfaction, they are well-positioned to shape the future of catalysis with their advanced gamma alumina catalyst solutions.